The Deep Dive: A Prefab Solution
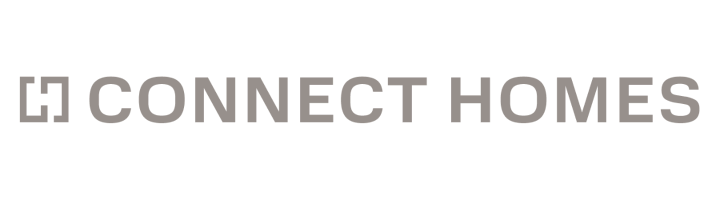
As any issue of Dwell proves, the choice of material or joinery method can transform a good project into a design for the ages. The Deep Dive is a forum where design and building pros can obsess over those details. Here we ask expert colleagues to share the inspiration behind house elements that delight clients—as well as the nitty-gritty information about how they were built.
When Jai Kumaran conceived a workshop and studio suite in Scappoose, Oregon, for himself and his partner Lindsay Merkle, they were met with unceremonious dismissals—and jarring estimates.
In the March/April feature, "A Couple Pining for Their Woodsy Upbringings Experiment With a Retreat in the Pacific Northwest," Lindsay recounts the difficulty of finding a contractor for the rural residence on their 20-acre ridgetop site. "People would drive up here and see the road—it’s an old logging road—and say, ‘Nope, not interested. It’s not possible,’" the homeowner told Dwell contributor Lauren Gallow.
Jai, a founding partner of the firm West of West, refrained from design plans until he was more certain of the material and labor resources at his disposal—and the early feedback from contractors, who were largely viewing the potential project as a wood-framed building, redirected his thinking toward prefabrication. "Some of our work at West of West is commercial-scaled buildings, where we had seen premade long-span steel strategies. So, I started thinking about those systems as a way to solve our problems."
When the architect reached out to manufacturer Web Steel Buildings Northwest, "They seemed to be totally capable and totally ready to go," Jai recalls, even though Web rarely worked in the residential sphere. "And since I wasn’t buying a kit of parts off the shelf, I was able to design what I wanted to design given their constraints—and constraints can be helpful from a designer’s perspective."
Using one of Web’s existing long-span steel systems, Jai arrived at a 3,000-square-foot gabled building whose components could be shipped to the property entirely on one truck. Because he and Lindsay wanted to erect the house on a site that did not require regrading, the dimensions of an already flat portion of landscape informed Jai’s process as well.
In addition to thinking of external parameters as creative boons, Jai says the benefits of a prefabricated steel structure were numerous. "One was speed: this idea that you can make something off-site, bring it in, and erect it very quickly was appealing. And the site itself was very hard to access, so minimizing the number of trips to the site and amount of time spent on site supported our mindset of restoring and naturalizing this property that had been treated poorly." He also believes that the move to steel echoes the decision that a regional farmer might make when building new storage or other facilities.
Of course, just as residential and commercial uses differ from one another, Jai worked with Web to domesticate its product. Whereas the interior of an agricultural building would likely be left raw, the second-floor living space demanded additional framing for walls and ceilings. Web’s in-house structural engineer thickened the primary steel beams in the studio floor to support that extra load.
Web’s system also included a secondary, lighter-gauge steel between the more robust columns and beams, whereas this steel would typically be fashioned into trusses to support the roof. "From an aesthetic standpoint, that was not something I was interested in," Jai explains. "It was too cluttered visually; it felt more like a warehouse. We ended up using a rigid frame system, which features a solid piece of material versus a truss strategy." The structure’s foundation is concrete slab on grade, with a mat footing under each column.
Exterior detailing proved to be the greatest challenge in adapting a commercial product for a residential program. "Web essentially has a kit of details and flashings that they use to finish inside and outside corners as well as ridges and eaves," Jai says, and while he specified these parts for Scappoose, the result "looked out of scale, and the quality of execution wasn’t there." Again, more like a warehouse.
Further validating Jai’s idea of prefabricated construction, commercial contractor Erectors, Inc. agreed to assemble the getaway without hesitation. "They saw a fun little project, and an opportunity to fill the gaps in its schedule between big projects," he says of Erectors’ quick decision. As for Web, the company’s interest in the project never ebbed, even after Jai expressed disappointment with the exterior trim. He designed more appropriate profiles for the most visible parts of the building’s skin, namely around its gabled ends, and Web realized the custom parts in turn.
We welcome your thoughts and illustrative projects. Reach out to pro@dwell.com.
Published
Topics
The Deep DiveGet the Pro Newsletter
What’s new in the design world? Stay up to date with our essential dispatches for design professionals.